Positive Material Identification (PMI)
XSI provides a variety of material identification solutions. Not all methodologies are crafted the same; our team of material experts asks the right questions ensuring you are receiving the information you need. In the field, PMI is accomplished by two primary technologies: X-ray fluorescens (XRF) or by spectroscopy (OES or LIBS). Each of the method has a different detection limits based on the the elements atomic weight.
It should be noted that Carbon content can only be obtained by means of spectroscopy or shavings for laboratory analysis.
X-Ray Fluorescence (XRF)
X-Ray Fluorescence (XRF) is a non-destructive analytical technique used to determine the elemental composition of materials. When a material is exposed to high-energy X-rays or gamma rays, it emits secondary (or fluorescent) X-rays that are characteristic of the elements present in the material.
Optical Emission Spectroscopy (OES)
Optical Emission Spectroscopy (OES) is a reliable technique for determining the elemental composition of metals. It involves exciting the atoms in a sample using an electrical discharge, which causes them to emit light at characteristic wavelengths.
Laser Induced Breakdown Spectroscopy (LIBS)
Laser Induced Breakdown Spectroscopy (LIBS) uses a highly energetic laser pulse to create a plasma on the sample surface, which atomizes and excites the material. The emitted light from the plasma is analyzed to determine the elemental composition.
Both OES and LIBS methods excel at detecting Carbon content, this enables XSI to perform CE calculation's, and differentiate between low and high carbon alloys.
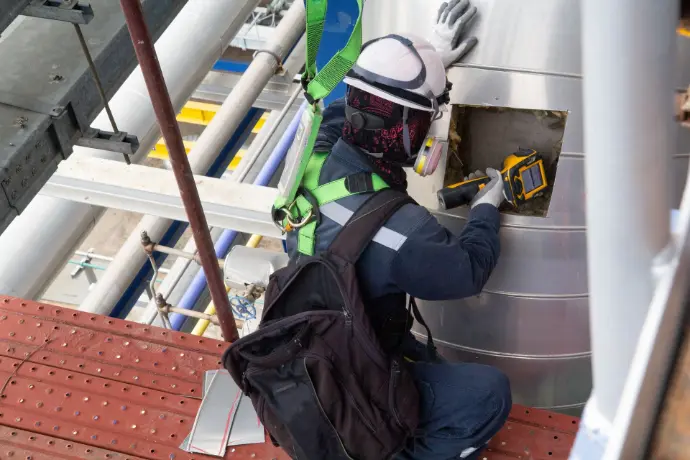
Hardness Testing
XSI's material training program aims to reduce error that is seen in portable hardness testing methods. Our training methods go into detail how the various hardness testing methods interact with different alloys. Hardness testing can be used to determine conformity to technical standards such as NACE MR0175, or confirmation of successful PWHT. We deploy two primary field testing methods, Telle Brinell and Ultrasonic Contact Impedance (UCI).
Brinell Hardness Testing
The Brinell Hardness Test measures the hardness of a material by pressing a hard indenter, usually a tungsten carbide ball, into the material's surface with a specified force. The size of the indent on the test specimen is then compared to the indent on the calibration standard to determine the materials HB number.
Due to the size of the indent and applied force, specimens have to have sufficient wall thickness to withstand the impact. Additional, placement of the ball often include both HAS and Parent Material hardness.
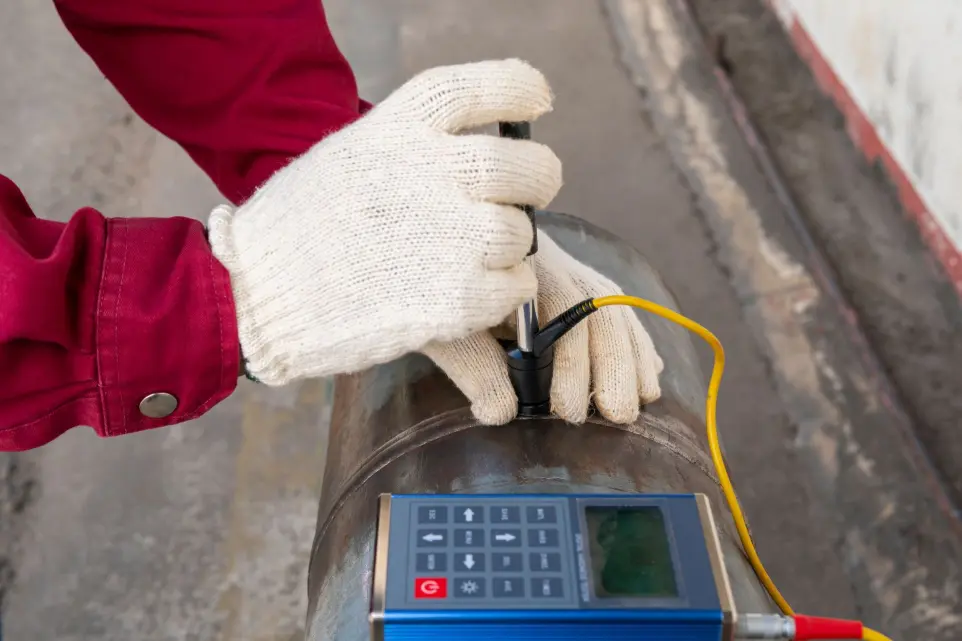
Ultrasonic Contact Impedance (UCI)
The Ultrasonic Contact Impedance (UCI) method involves using a vibrating rod with a Vickers diamond tip to measure the indentation depth in the material. As UCI utilizes ultrasonics its imperative the correct calibration standards are used.
As the indentation is relatively small, UCI excels at determining areas of localized hardness such as in the HAZ.
Hardness test methods are compliant with NACE, ASME, CSA and ISO standards.
Ferrite Testing
Applications
Ferrite testing measures the ferrite content in stainless steels and other alloys, which is crucial for predicting the material's performance in various environments. Ferrite testers measure the ferrite content either by FN or % by inducing a magnetic field into the specimen.
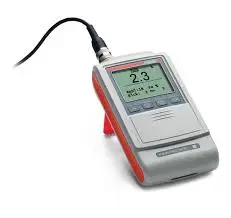
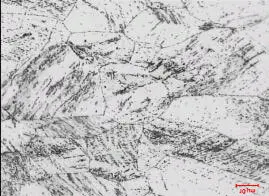
In-Situ Metallography
Microstructural Assessments
In-situ metallography allows for on-site examination of materials without the need for sample removal. This technique is ideal for evaluating grain size, phase distribution, and the presence of inclusions or defects.
XSI provides a stage training approach, with technicians graduating to more critical etching techniques.
Common tests include:
- Creep Damage Assessment: For high-temperature components in power plants.
- Graphitization: For evaluating the microstructure of cast irons.
- Sigma Phase Detection: In stainless steels to prevent embrittlement.
- Grain Growth Analysis: For materials exposed to high temperatures.
- Weld Quality Inspection: To ensure the integrity of welds in critical structures.